Вафлиди кесүү технологиясы жарым өткөргүчтөрдү өндүрүү процессиндеги маанилүү кадам катары чиптин иштешине, түшүмдүүлүгүнө жана өндүрүштүк чыгымдарына түздөн-түз байланыштуу.
#01 Вафельди кесүүнүн негиздери жана мааниси
1.1 Вафельди кесүүнүн аныктамасы
Вафлиди кесүү (ошондой эле скрипинг деп аталат) жарым өткөргүчтөрдү өндүрүүдөгү маанилүү кадам болуп саналат, ал кайра иштетилген пластиналарды бир нече жеке калыптарга бөлүүгө багытталган. Бул өлүктөр, адатта, толук чынжыр иштешин камтыйт жана акырында электрондук аппараттарды өндүрүүдө колдонулган негизги компоненттери болуп саналат. Чиптин конструкциялары татаалдашып, өлчөмдөр кичирейген сайын, вафлиди кесүү технологиясы үчүн тактык жана эффективдүү талаптар барган сайын катаал болуп баратат.
Практикалык операцияларда пластинкаларды кесүү, адатта, ар бир калыптын бүтүн бойдон жана толук иштешин камсыз кылуу үчүн алмаз бычактар сыяктуу жогорку тактыктагы куралдарды колдонот. Негизги кадамдарга кесүү алдында даярдоо, кесүү процессинде так контролдоо жана кесүүдөн кийин сапатты текшерүү кирет.
Кесүүдөн мурун, вафли так кесүү жолдорун камсыз кылуу үчүн белгилениши жана жайгаштырылышы керек. Кесүү учурунда пластинкага зыян келтирбөө үчүн инструменттин басымы жана ылдамдыгы сыяктуу параметрлер катуу көзөмөлгө алынышы керек. Кесилгенден кийин, ар бир чиптин иштөө стандарттарына жооп бериши үчүн комплекстүү сапат текшерүүлөрү жүргүзүлөт.
Вафлиди кесүү технологиясынын негизги принциптери кесүүчү жабдууларды тандоону жана процесстин параметрлерин орнотууну гана эмес, ошондой эле материалдардын механикалык касиеттери менен мүнөздөмөлөрүнүн кесүү сапатына таасирин да камтыйт. Мисалы, аз к-диэлектрик кремний пластиналары, алардын механикалык касиеттери төмөн болгондуктан, кесүү учурунда стресс концентрациясына өтө сезгич болуп, майдалоо жана жарылып кетүү сыяктуу кемчиликтерге алып келет. Төмөн-к материалдардын аз катуулук жана морттугу аларды механикалык күчтүн же жылуулук стрессинин астында, айрыкча кесүү учурунда структуралык бузулууга көбүрөөк жакын кылат. Курал менен пластинанын бетинин ортосундагы байланыш, жогорку температура менен бирге стресстин концентрациясын андан ары күчөтүшү мүмкүн.
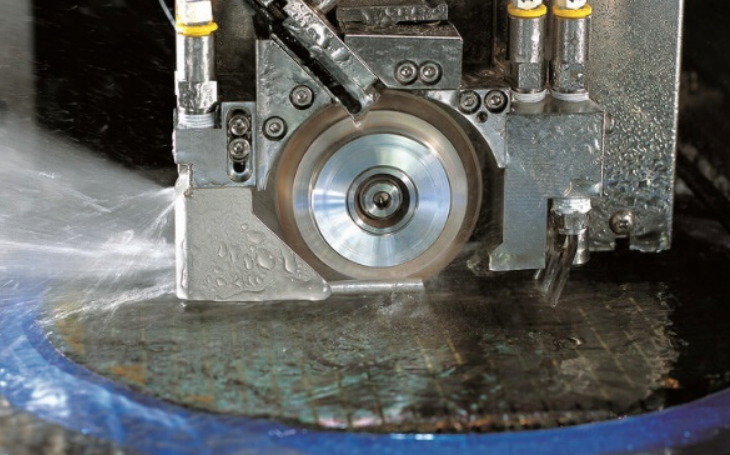
Материал таануудагы жетишкендиктер менен пластинкаларды кесүү технологиясы салттуу кремнийге негизделген жарым өткөргүчтөрдүн чегинен чыгып, галлий нитриди (GaN) сыяктуу жаңы материалдарды камтыйт. Бул жаңы материалдар өзүнүн катуулугунан жана структуралык касиеттеринен улам, кесүүчү шаймандарды жана техниканы андан ары өркүндөтүүнү талап кылып, кесүү процесстери үчүн жаңы кыйынчылыктарды жаратат.
Жарым өткөргүч өнөр жайындагы маанилүү процесс катары, пластинкаларды кесүү өнүгүп жаткан талаптарга жана технологиялык жетишкендиктерге жооп катары оптималдаштырууну улантууда, келечектеги микроэлектроника жана интегралдык микросхема технологиялары үчүн негиз салуу.
Вафлиди кесүү технологиясын өркүндөтүү жардамчы материалдарды жана аспаптарды иштеп чыгуудан да ашып кетет. Алар ошондой эле процессти оптималдаштырууну, жабдуулардын иштешин жакшыртууну жана кесүү параметрлерин так көзөмөлдөөнү камтыйт. Бул жетишкендиктер жарым өткөргүч өнөр жайынын кичинекей өлчөмдөргө, жогорку интеграцияга жана татаал чип структураларына болгон муктаждыгын канааттандырып, пластинкаларды кесүү процессинде жогорку тактыкты, натыйжалуулукту жана туруктуулукту камсыз кылууга багытталган.
жакшыртуу аймагы | Конкреттүү чаралар | Эффекттер |
Процессти оптималдаштыруу | - Баштапкы даярдыктарды өркүндөтүү, мисалы, пластинанын так жайгашуусу жана жолду пландаштыруу. | - Кесүү каталарын азайтуу жана туруктуулукту жакшыртуу. |
- Кесүү каталарын азайтуу жана туруктуулукту жогорулатуу. | - Аспаптын басымын, ылдамдыгын жана температурасын жөнгө салуу үчүн реалдуу убакыт режиминде мониторинг жүргүзүү жана кайтарым байланыш механизмдерин кабыл алыңыз. | |
- Вафли сынуу ылдамдыгын төмөндөтүп, чиптин сапатын жакшыртуу. | ||
Жабдуулардын натыйжалуулугун жогорулатуу | - жогорку тактыктагы механикалык системаларды жана алдыңкы автоматташтыруу башкаруу технологиясын колдонуу. | - Кесүү тактыгын жогорулатуу жана материалдык ысырапты азайтуу. |
- Катуулугу жогору материал пластинкаларына ылайыктуу лазердик кесүү технологиясын киргизүү. | - өндүрүштүн натыйжалуулугун жогорулатуу жана кол каталарды азайтуу. | |
- Автоматтык мониторинг жана жөнгө салуу үчүн жабдууларды автоматташтырууну жогорулатуу. | ||
Так Параметр башкаруу | - Кесүү тереңдиги, ылдамдык, шайман түрү жана муздатуу ыкмалары сыяктуу параметрлерди жакшылап тууралаңыз. | - өлчөм бүтүндүгүн жана электр натыйжалуулугун камсыз кылуу. |
- Вафли материалына, калыңдыгына жана структурасына жараша параметрлерди ыңгайлаштыруу. | - Түшүмдүүлүктү жогорулатуу, материалдык калдыктарды азайтуу жана өндүрүштүн наркын төмөндөтүү. | |
Стратегиялык мааниси | - Дайыма жаңы технологиялык жолдорду изилдөө, процесстерди оптималдаштыруу жана рыноктун талаптарын канааттандыруу үчүн жабдуулардын мүмкүнчүлүктөрүн жогорулатуу. | - Жаңы материалдарды жана алдыңкы чип конструкцияларын иштеп чыгууну колдоо, чип өндүрүшүнүн кирешелүүлүгүн жана натыйжалуулугун жогорулатуу. |
1.2 Вафельди кесүүнүн мааниси
Вафлиди кесүү жарым өткөргүчтөрдү өндүрүү процессинде маанилүү ролду ойнойт, кийинки кадамдарга, ошондой эле акыркы продукттун сапатына жана натыйжалуулугуна түздөн-түз таасир этет. Анын маанилүүлүгүн төмөнкүчө чагылдырууга болот:
Биринчиден, кесүүнүн тактыгы жана ырааттуулугу чиптин түшүмдүүлүгүн жана ишенимдүүлүгүн камсыз кылуунун ачкычы болуп саналат. Өндүрүш учурунда пластиналар жеке микросхемаларга (өлүктөргө) так бөлүнүшү керек болгон көптөгөн татаал схемалык түзүлүштөрдү түзүү үчүн бир нече кайра иштетүү кадамдарынан өтүшөт. Эгерде кесүү процессинде тегиздөө же кесүүдө олуттуу каталар болсо, схемалар бузулуп, чиптин иштөөсүнө жана ишенимдүүлүгүнө таасир этиши мүмкүн. Ошондуктан, жогорку тактыктагы кесүү технологиясы ар бир чиптин бүтүндүгүн гана камсыз кылбастан, ошондой эле ички схемалардын бузулушун алдын алып, жалпы түшүмдүүлүктү жогорулатат.
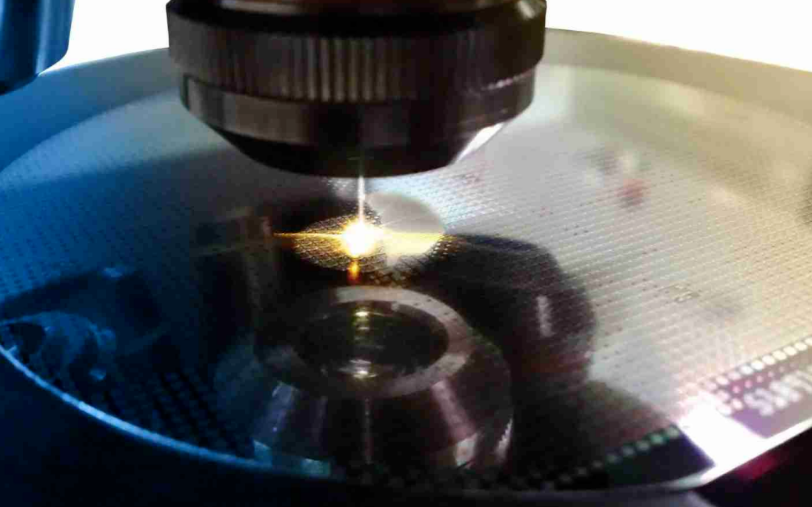
Экинчиден, вафлиди кесүү өндүрүштүн натыйжалуулугуна жана өздүк наркты көзөмөлдөөгө олуттуу таасирин тийгизет. Өндүрүш процессиндеги чечүүчү кадам катары анын натыйжалуулугу кийинки кадамдардын жүрүшүнө түздөн-түз таасир этет. Кесүү процессин оптималдаштыруу, автоматташтыруу деңгээлин жогорулатуу жана кесүү ылдамдыгын жакшыртуу менен жалпы өндүрүштүн натыйжалуулугун бир топ жогорулатууга болот.
Башка жагынан алганда, кесүү учурунда материалдык ысырапкорчулук чыгымдарды башкаруу үчүн маанилүү фактор болуп саналат. Өркүндөтүлгөн кесүү технологияларын колдонуу кесүү процессинде ашыкча материалдык жоготууларды азайтпастан, ошондой эле пластиналарды колдонууну көбөйтөт, ошону менен өндүрүштүн баасын төмөндөтөт.
Жарым өткөргүч технологиясынын жетишкендиктери менен пластинкалардын диаметрлери көбөйө берет жана чынжырдын тыгыздыгы ошого жараша жогорулап, кесүү технологиясына жогорку талаптарды коюп жатат. Чоңураак пластиналар кесүү жолдорун так көзөмөлдөөнү талап кылат, өзгөчө тыгыздыгы жогору схема аймактарында, ал тургай кичинекей четтөөлөр да бир нече микросхемалардын бузулушуна алып келиши мүмкүн. Кошумчалай кетсек, чоңураак пластиналар кесүү линияларын жана татаал процесс кадамдарын камтыйт, бул кыйынчылыктарга жооп берүү үчүн кесүү технологияларынын тактыгын, ырааттуулугун жана натыйжалуулугун андан ары жакшыртууну талап кылат.
1.3 Вафельди кесүү процесси
Вафлиди кесүү процесси даярдоо фазасынан тартып акыркы сапатты текшерүүгө чейинки бардык кадамдарды камтыйт, ар бир этап кесилген чиптердин сапатын жана иштешин камсыз кылуу үчүн маанилүү. Төмөндө ар бир этаптын деталдуу түшүндүрмө болуп саналат.
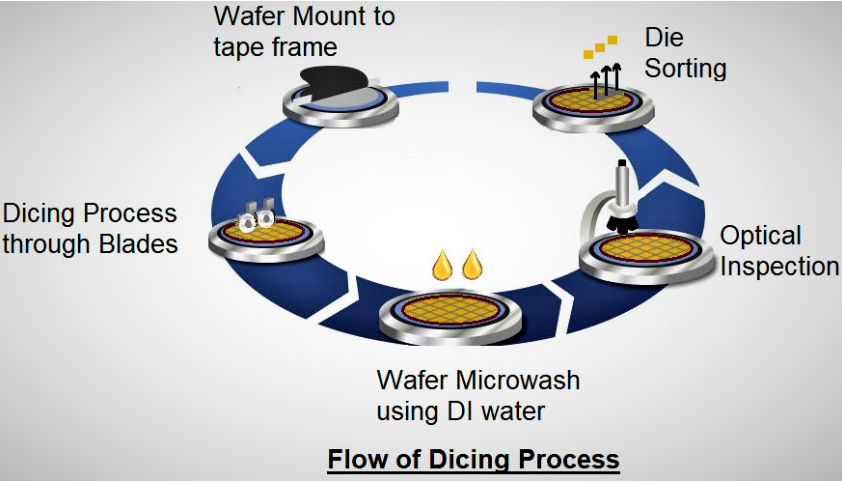
Фаза | Detailed Description |
Даярдоо фазасы | -Вафли тазалоо: Таза бетти камсыз кылуу үчүн кирлерди, бөлүкчөлөрдү жана булгоочу заттарды жок кылуу үчүн жогорку тазалыктагы сууну жана атайын тазалоочу каражаттарды ультраүн же механикалык тазалоо менен бирге колдонуңуз. -Так жайгаштыруу: Вафлиди кесүү жолдору боюнча так бөлүштүрүүнү камсыз кылуу үчүн жогорку тактыктагы жабдууларды колдонуңуз. -Wafer Fixation: Кесүү учурунда туруктуулукту сактоо үчүн, титирөөдөн же кыймылдан зыян келтирбөө үчүн пластинаны лента рамкасына бекитиңиз. |
Кесүү фазасы | -Blade Dicing: Физикалык кесүү үчүн жогорку ылдамдыкта айлануучу алмаз менен капталган бычактарды колдонуңуз, кремний негизиндеги материалдарга ылайыктуу жана үнөмдүү. -Лазердик кесүү: Байланышсыз кесүү үчүн жогорку энергиялуу лазер нурларын колдонуңуз, галлий нитриди сыяктуу морт же жогорку катуулуктагы материалдар үчүн идеалдуу, жогорку тактыкты жана материалды аз жоготууну сунуш кылат. -New Technologies: Жылуулук таасир эткен аймактарды азайтуу менен эффективдүүлүктү жана тактыкты андан ары жогорулатуу үчүн лазердик жана плазмалык кесүү технологияларын киргизүү. |
Тазалоо фазасы | - Кесүү учурунда пайда болгон калдыктарды жана чаңды тазалоо үчүн, кийинки процесстерге же микросхемалардын электр иштешине таасирин тийгизбөө үчүн деионизацияланган сууну (DI суу) жана атайын тазалоочу каражаттарды колдонуңуз. - Жогорку тазалыктагы DI суу жаңы булгоочу заттарды киргизүүдөн качат, таза вафли чөйрөсүн камсыз кылат. |
Текшерүү фазасы | -Оптикалык текшерүү: Кемчиликтерди тез аныктоо, кесилген чиптерде эч кандай жарака же чип болбоо, текшерүүнүн натыйжалуулугун жогорулатуу жана адам катасын азайтуу үчүн AI алгоритмдери менен айкалышкан оптикалык аныктоо системаларын колдонуңуз. -Dimension Measurement: Чип өлчөмдөрү дизайн спецификацияларына жооп берерин текшериңиз. -Электр натыйжалуулугун сыноо: Критикалык микросхемалардын электрдик көрсөткүчтөрүнүн стандарттарга жооп беришин камсыз кылуу, кийинки колдонмолордо ишенимдүүлүктү камсыз кылуу. |
Сорттоо фазасы | - Тасма алкагынан квалификациялуу микросхемаларды бөлүп алуу үчүн роботторду же вакуумдук соргучтарды колдонуңуз жана аларды аткаруунун негизинде автоматтык түрдө сорттоп, өндүрүштүн натыйжалуулугун жана ийкемдүүлүгүн камсыз кылып, тактыкты жогорулатыңыз. |
Вафли кесүү процесси вафлиди тазалоону, жайгаштырууну, кесүүнү, тазалоону, текшерүүнү жана сорттоону камтыйт, ар бир кадам маанилүү. Автоматташтыруу, лазердик кесүү жана AI текшерүү технологияларындагы жетишкендиктер менен заманбап пластина кесүү системалары жогорку тактыкка, ылдамдыкка жана материалдык жоготууга жетише алат. Келечекте, лазер жана плазма сыяктуу жаңы кесүү технологиялары бара-бара татаал чип конструкцияларынын муктаждыктарын канааттандыруу үчүн салттуу бычак кесүүнү алмаштырып, жарым өткөргүчтөрдү өндүрүү процесстерин андан ары өнүктүрүүгө түрткү берет.
Вафли кесүү технологиясы жана анын принциптери
Сүрөттө пластинаны кесүүнүн үч жалпы технологиясы көрсөтүлгөн:Blade Dicing,Лазердик кесүү, жанаPlasma Dicing. Төмөндө бул үч техниканын деталдуу талдоосу жана кошумча түшүндүрмөсү келтирилген:
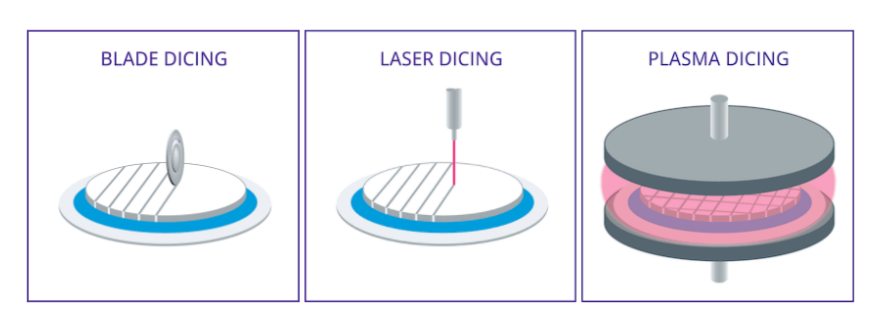
Жарым өткөргүч өндүрүшүндө пластинаны кесүү вафлидин калыңдыгына жараша туура кесүү ыкмасын тандоону талап кылган маанилүү кадам болуп саналат. Биринчи кадам пластинка калыңдыгын аныктоо болуп саналат. Эгерде пластинкалардын калыңдыгы 100 микрондон ашса, кесүү ыкмасы катары бычакты кесүү тандалышы мүмкүн. Эгерде бычакты кесүү ылайыксыз болсо, сыныктарды кесүү ыкмасын колдонсо болот, ага скрипт кесүү жана бычак кесүү ыкмалары кирет.
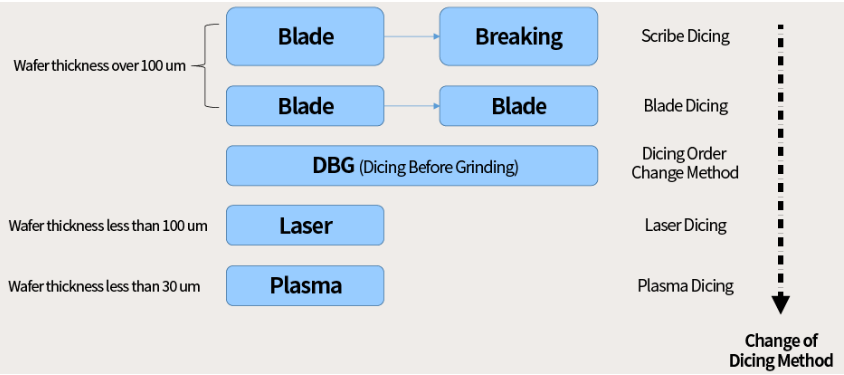
Вафли калыңдыгы 30 жана 100 микрондун ортосунда болгондо, DBG (Жаргылдатуудан мурун Dice) ыкмасы сунушталат. Бул учурда, эң жакшы натыйжаларга жетүү үчүн кесүүнү, бычакты кесүүнү же кесүү ырааттуулугун тууралоону тандаса болот.
Калыңдыгы 30 микрондон ашпаган ультра жука пластиналар үчүн лазердик кесүү анын жука пластиналарды ашыкча зыян келтирбестен так кесүү жөндөмдүүлүгүнөн артыкчылыктуу ыкма болуп калат. Лазердик кесүү конкреттүү талаптарга жооп бере албаса, альтернатива катары плазмалык кесүү колдонулушу мүмкүн. Бул схема ар кандай жоондуктун шарттарында эң ылайыктуу пластинка кесүү технологиясын тандоону камсыз кылуу үчүн чечим кабыл алуунун так жолун камсыз кылат.
2.1 Механикалык кесүү технологиясы
Механикалык кесүү технологиясы вафлиди кесүүдө салттуу ыкма болуп саналат. Негизги принцип пластинаны кесүү үчүн кесүүчү курал катары жогорку ылдамдыкта айлануучу алмазды жылмалоо дөңгөлөктөрүн колдонуу болуп саналат. Негизги жабдуулардын курамына аба көтөрүүчү шпиндель кирет, ал алмазды жылмалоочу дөңгөлөк куралын алдын ала аныкталган кесүү жолу боюнча так кесүүнү же оюуларды аткаруу үчүн жогорку ылдамдыкта айдайт. Бул технология өзүнүн арзан баасына, жогорку натыйжалуулугуна жана кеңири колдонулушуна байланыштуу өнөр жайда кеңири колдонулат.
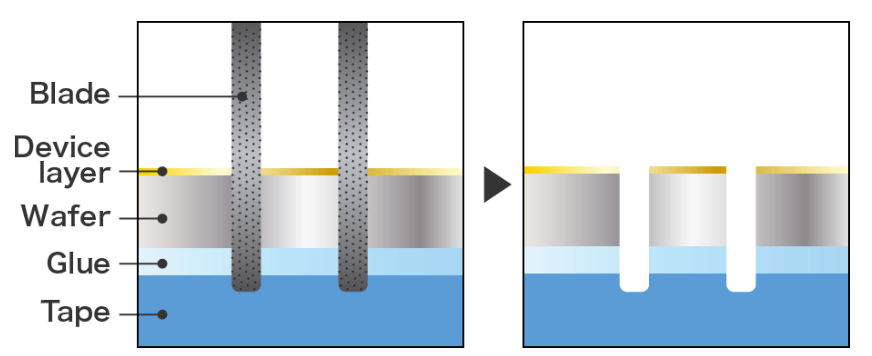
Артыкчылыктары
Алмазды майдалоочу дөңгөлөк шаймандарынын жогорку катуулугу жана эскирүү туруктуулугу механикалык кесүү технологиясына ар кандай пластинка материалдарынын кесүү муктаждыктарына ыңгайлашууга мүмкүндүк берет, мейли салттуу кремнийге негизделген материалдар же жаңы кошулма жарым өткөргүчтөр. Анын иштеши жөнөкөй, салыштырмалуу төмөн техникалык талаптар менен, андан ары массалык өндүрүштө анын популярдуулугун жогорулатуу. Кошумчалай кетсек, лазердик кесүү сыяктуу башка кесүү ыкмаларына салыштырмалуу, механикалык кесүү контролдонуучу чыгымдарга ээ, бул жогорку көлөмдөгү өндүрүш муктаждыктарына ылайыктуу.
Чектөөлөр
Анын көптөгөн артыкчылыктарына карабастан, механикалык кесүү технологиясы да чектөөлөргө ээ. Биринчиден, аспап менен пластинанын ортосундагы физикалык байланыштан улам, кесүү тактыгы салыштырмалуу чектелген, бул көбүнчө чиптин кийинки пакеттөө жана тестирлөөнүн тактыгына таасир эте турган өлчөмдүү четтөөлөргө алып келет. Экинчиден, майдалоо жана жаракалар сыяктуу кемчиликтер механикалык кесүү процессинде оңой эле пайда болушу мүмкүн, бул түшүмдүүлүккө гана таасирин тийгизбестен, чиптердин ишенимдүүлүгүнө жана иштөө мөөнөтүнө терс таасирин тийгизиши мүмкүн. Механикалык стресстен келип чыккан зыян, өзгөчө, жогорку тыгыздыктагы чиптерди өндүрүү үчүн зыяндуу, айрыкча морт материалдарды кескенде, бул маселелер көбүрөөк орун алган.
Технологиялык өркүндөтүү
Бул чектөөлөрдү жоюу үчүн, изилдөөчүлөр тынымсыз механикалык кесүү жараянын оптималдаштыруу. Негизги өркүндөтүүлөр кесүү тактыгын жана бышыктыгын жакшыртуу үчүн майдалоочу дөңгөлөктөрдүн дизайнын жана материалды тандоону жакшыртууну камтыйт. Кошумчалай кетсек, кесүүчү жабдуулардын структуралык дизайнын жана башкаруу системаларын оптималдаштыруу кесүү процессинин туруктуулугун жана автоматташтыруусун андан ары жакшыртты. Бул жетишкендиктер адамдын аракеттеринен келип чыккан каталарды азайтат жана кыскартуулардын ырааттуулугун жакшыртат. Кесүү процессиндеги аномалияларга реалдуу убакыт режиминде мониторинг жүргүзүү үчүн алдыңкы текшерүү жана сапатты көзөмөлдөө технологияларын ишке киргизүү да кесүүнүн ишенимдүүлүгүн жана түшүмдүүлүгүн бир топ жакшыртты.
Келечектеги өнүгүү жана жаңы технологиялар
Механикалык кесүү технологиясы вафлиди кесүүдө дагы эле маанилүү орунду ээлегени менен, жарым өткөргүч процесстери өнүккөн сайын жаңы кесүү технологиялары тездик менен өнүгүп жатат. Мисалы, термикалык лазердик кесүү технологиясын колдонуу механикалык кесүүдө тактык жана кемчилик маселелерине жаңы чечимдерди берет. Бул контактсыз кесүү ыкмасы пластинкадагы физикалык стрессти азайтып, майдалоо жана крекинг учурларын бир топ төмөндөтөт, айрыкча морт материалдарды кескенде. Келечекте, механикалык кесүү технологиясын жаңы пайда болгон кесүү ыкмалары менен интеграциялоо жарым өткөргүчтөрдү өндүрүүнү көбүрөөк мүмкүнчүлүктөрдү жана ийкемдүүлүк менен камсыз кылып, өндүрүштүн натыйжалуулугун жана чиптин сапатын андан ары жогорулатууга мүмкүндүк берет.
Жыйынтыктап айтканда, механикалык кесүү технологиясы белгилүү бир кемчиликтерге ээ болсо да, үзгүлтүксүз технологиялык өркүндөтүүлөр жана анын жаңы кесүү ыкмалары менен интеграциясы жарым өткөргүчтөрдү өндүрүүдө дагы эле маанилүү ролду ойноого жана келечектеги процесстерде өзүнүн атаандаштыкка жөндөмдүүлүгүн сактоого мүмкүндүк берет.
2.2 Лазердик кесүү технологиясы
Лазердик кесүү технологиясы, пластинкаларды кесүүдө жаңы ыкма катары, анын жогорку тактыгына, механикалык байланыштын бузулушуна жана тез кесүү жөндөмдүүлүгүнө байланыштуу жарым өткөргүч өнөр жайында акырындык менен кеңири көңүл бура баштады. Бул технология лазер нурунун жогорку энергия тыгыздыгын жана фокустоо жөндөмүн вафли материалынын бетинде кичинекей жылуулук таасир этүүчү аймакты түзүү үчүн колдонот. Лазердик нур пластинкага колдонулганда, пайда болгон термикалык стресс материалдын так кесилишине жетишип, белгиленген жерде сынып кетишине алып келет.
Лазердик кесүү технологиясынын артыкчылыктары
• Жогорку тактык: Лазердик нурдун так жайгаштыруу жөндөмдүүлүгү заманбап жогорку тактыктагы, жогорку тыгыздыктагы интегралдык микросхемалардын өндүрүшүнүн талаптарына жооп берген микрон же ал тургай нанометр деңгээлинде кесүү тактыгына мүмкүндүк берет.
• Механикалык байланыш жок: Лазердик кесүү пластинка менен физикалык байланыштан качат, механикалык кесүүдөгү жалпы маселелердин алдын алуу, мисалы, чип алуу жана жаракалоо, микросхемалардын түшүмдүүлүгүн жана ишенимдүүлүгүн кыйла жакшыртат.
• Тез кесүү ылдамдыгы: Лазердик кесүүнүн жогорку ылдамдыгы өндүрүштүн натыйжалуулугун жогорулатууга өбөлгө түзөт, аны ири масштабдуу, жогорку ылдамдыктагы өндүрүш сценарийлери үчүн өзгөчө ылайыктуу кылат.
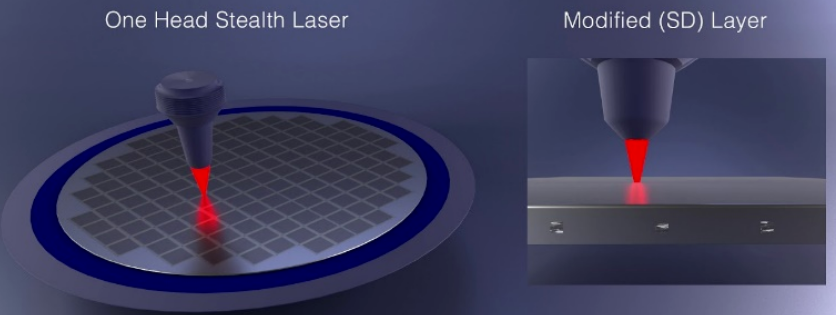
Кыйынчылыктар
• Жабдуулардын жогорку баасы: Лазердик кесүү жабдыктары үчүн баштапкы инвестиция, өзгөчө чакан жана орто өндүрүш ишканалары үчүн экономикалык басымды жаратат.
• Процессти комплекстүү башкаруу: Лазердик кесүү бир нече параметрлерди так көзөмөлдөөнү талап кылат, анын ичинде энергиянын тыгыздыгы, фокустун абалы жана кесүү ылдамдыгы, процессти татаал кылуу.
• Жылуулук таасир эткен зона маселелери: Лазердик кесүүнүн контактсыз мүнөзү механикалык зыянды азайтса да, жылуулук таасир эткен зонадан (HAZ) келип чыккан жылуулук стресс пластинка материалынын касиеттерине терс таасирин тийгизиши мүмкүн. Бул эффектти минималдаштыруу үчүн процессти андан ары оптималдаштыруу керек.
Технологиялык жакшыртуу багыттары
Бул көйгөйлөрдү чечүү үчүн изилдөөчүлөр жабдуулардын баасын төмөндөтүүгө, кесүүнүн натыйжалуулугун жогорулатууга жана процесстин агымын оптималдаштырууга басым жасашууда.
• Натыйжалуу лазерлер жана оптикалык системалар: Эффективдүү лазерлерди жана өнүккөн оптикалык системаларды иштеп чыгуу менен, кесүү тактыгын жана ылдамдыгын жогорулатуу менен бирге жабдуулардын баасын төмөндөтүүгө болот.
• Процесс параметрлерин оптималдаштыруу: Лазерлердин жана пластинкалардын материалдарынын ортосундагы өз ара аракеттешүү боюнча терең изилдөөлөр жылуулук таасир эткен аймакты азайтуучу процесстерди өркүндөтүү, ошону менен кесүү сапатын жакшыртуу үчүн жүргүзүлүүдө.
• Интеллектуалдык башкаруу системалары: Интеллектуалдык башкаруу технологияларын иштеп чыгуу лазердик кесүү процессин автоматташтыруу жана оптималдаштыруу, анын туруктуулугун жана ырааттуулугун жогорулатууга багытталган.
Лазердик кесүү технологиясы өзгөчө ультра жука пластинкаларда жана жогорку тактыктагы кесүү сценарийлеринде натыйжалуу. Вафли өлчөмдөрү көбөйүп, схеманын тыгыздыгы жогорулаган сайын, салттуу механикалык кесүү ыкмалары заманбап жарым өткөргүч өндүрүшүнүн жогорку тактык жана эффективдүү талаптарын канааттандыруу үчүн күрөшөт. Өзүнүн уникалдуу артыкчылыктарынан улам лазердик кесүү бул тармактарда артыкчылыктуу чечимге айланууда.
Лазердик кесүү технологиясы дагы эле жабдуулардын жогорку баасы жана процесстин татаалдыгы сыяктуу кыйынчылыктарга туш болсо да, анын жогорку тактыктагы жана контактсыз зыяндагы уникалдуу артыкчылыктары аны жарым өткөргүч өндүрүшүндө өнүктүрүүнүн маанилүү багыты болуп саналат. Лазердик технология жана акылдуу башкаруу системалары алдыга жылган сайын, лазердик кесүү пластинкаларды кесүүнүн натыйжалуулугун жана сапатын андан ары жакшыртуу, жарым өткөргүч өнөр жайынын үзгүлтүксүз өнүгүшүн шарттайт.
2.3 Плазмалык кесүү технологиясы
Плазмалык кесүү технологиясы, пайда болгон вафлиди кесүү ыкмасы катары, акыркы жылдары олуттуу көңүл буруп жатат. Бул технология плазма нурунун энергиясын, ылдамдыгын жана кесүү жолун көзөмөлдөп, оптималдуу кесүү натыйжаларына жетишүү аркылуу пластиналарды так кесүү үчүн жогорку энергиялуу плазмалык нурларды колдонот.
Иштөө принциби жана артыкчылыктары
Плазмалык кесүү процесси жабдуулар тарабынан түзүлгөн жогорку температурадагы, жогорку энергиялуу плазма нуруна таянат. Бул нур вафли материалын өтө кыска убакыттын ичинде эрүү же буулануу чекитине чейин ысытып, тез кесүүгө мүмкүндүк берет. Салттуу механикалык же лазердик кесүү менен салыштырганда, плазма кесүү ылдамыраак жана кичине жылуулуктан жабыркаган аймакты жаратып, кесүү учурунда жаракалардын жана зыяндын пайда болушун натыйжалуу азайтат.
Практикалык колдонмолордо плазма кесүү технологиясы татаал формадагы вафлилерди иштетүүдө өзгөчө чебер. Анын жогорку энергиялуу, жөнгө салынуучу плазма нуру туура эмес формадагы пластиналарды жогорку тактык менен оңой кесип алат. Ошондуктан, микроэлектроника өндүрүшүндө, өзгөчө жогорку чендеги микросхемалардын жекелештирилген жана чакан сериялуу өндүрүшүндө, бул технология кеңири колдонуу үчүн чоң келечекти көрсөтөт.
Кыйынчылыктар жана чектөөлөр
Плазмалык кесүү технологиясынын көптөгөн артыкчылыктарына карабастан, ал кээ бир кыйынчылыктарга да дуушар болот.
• Татаал процесс: Плазма кесүү жараяны татаал жана камсыз кылуу үчүн жогорку тактыктагы жабдууларды жана тажрыйбалуу операторлорду талап кылаткесүүдөгү тактык жана туруктуулук.
• Экологиялык көзөмөл жана коопсуздук: Плазма нурунун жогорку температура, жогорку энергиялуу мүнөзү катуу экологиялык көзөмөлдү жана коопсуздук чараларын талап кылат, бул ишке ашыруунун татаалдыгын жана баасын жогорулатат.
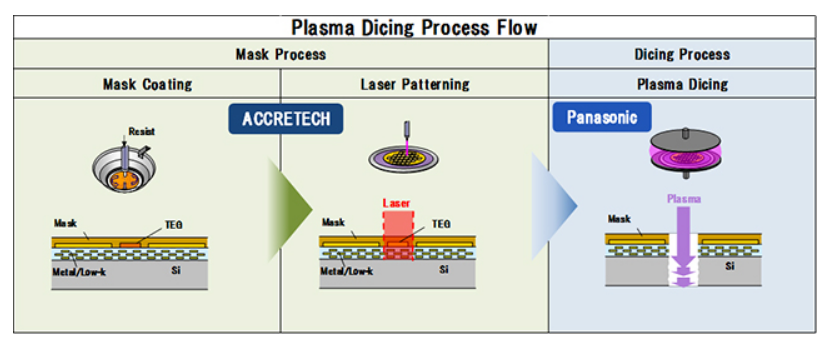
Келечектеги өнүгүү багыттары
Технологиялык жетишкендиктер менен плазмалык кесүү менен байланышкан кыйынчылыктар акырындык менен жоюлат деп күтүлүүдө. Акылдуураак жана туруктуу кесүүчү жабдууларды иштеп чыгуу менен, кол менен иштөөгө көз карандылыкты азайтып, ошону менен өндүрүштүн натыйжалуулугун жогорулатууга болот. Ошол эле учурда процесстин параметрлерин жана кесүү чөйрөсүн оптималдаштыруу коопсуздук тобокелдиктерин жана операциялык чыгымдарды азайтууга жардам берет.
Жарым өткөргүчтөр тармагында пластинкаларды кесүү жана кесүү технологиясындагы инновациялар тармактын өнүгүшү үчүн абдан маанилүү. Плазмалык кесүү технологиясы, анын жогорку тактыгы, натыйжалуулугу жана татаал пластинка формаларын иштетүүгө жөндөмдүүлүгү менен бул тармакта олуттуу жаңы оюнчу болуп чыкты. Кээ бир кыйынчылыктар дагы эле болсо да, бул маселелер акырындык менен технологиялык инновацияларды улантуу менен чечилип, жарым өткөргүчтөрдү өндүрүүгө көбүрөөк мүмкүнчүлүктөрдү жана мүмкүнчүлүктөрдү алып келет.
Плазмалык кесүү технологиясын колдонуу келечеги кең жана келечекте жарым өткөргүчтөрдү өндүрүүдө маанилүү ролду ойнойт деп күтүлүүдө. Үзгүлтүксүз технологиялык инновациялар жана оптималдаштыруу аркылуу плазмалык кесүү учурдагы көйгөйлөрдү чечпестен, жарым өткөргүч өнөр жайынын өсүшүнүн кубаттуу кыймылдаткычына айланат.
2.4 Кесүү сапаты жана таасир этүүчү факторлор
Wafer кесүү сапаты кийинки чип таңгактоо, тестирлөө жана акыркы продукттун жалпы аткаруу жана ишенимдүүлүгү үчүн абдан маанилүү болуп саналат. Кесүү учурунда кездешкен жалпы маселелерге жаракалар, чиптер жана кесүү четтөөлөр кирет. Бул көйгөйлөр чогуу иштеген бир нече факторлордун таасиринде турат.
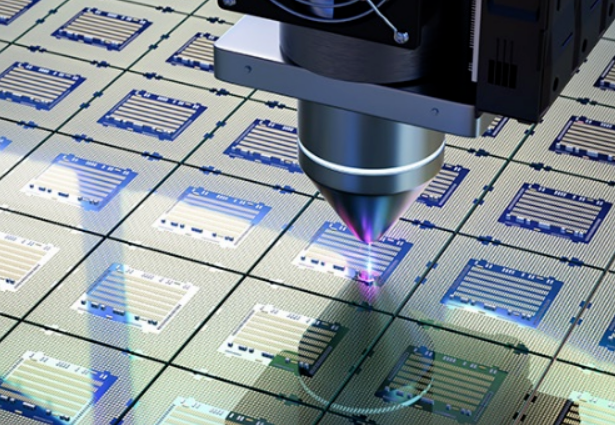
Категория | Мазмун | Таасири |
Процесс параметрлери | Кесүү ылдамдыгы, тоют ылдамдыгы жана кесүү тереңдиги кесүү процессинин туруктуулугуна жана тактыгына түздөн-түз таасир этет. Туура эмес орнотуулар стресстин топтолушуна жана ашыкча ысыктык зонасына алып келиши мүмкүн, натыйжада жаракалар жана чиптер пайда болот. Вафли материалына, калыңдыгына жана кесүү талаптарына ылайык параметрлерди тууралоо кесүү каалаган натыйжаларга жетишүүнүн ачкычы болуп саналат. | Процесстин туура параметрлери так кесүүнү камсыз кылат жана жаракалар жана чиптер сыяктуу кемчиликтердин пайда болуу коркунучун азайтат. |
Жабдуулар жана материалдык факторлор | -Бычактын сапаты: Бычактын материалы, катуулугу жана эскирүү туруктуулугу кесүү процессинин жылмакайлыгына жана кесилген беттин тегиздигине таасир этет. Начар сапаттагы бычактар сүрүлүүнү жана жылуулук стрессти күчөтүп, жаракаларга же чиптерге алып келиши мүмкүн. Туура бычак материалды тандоо абдан маанилүү. -Муздаткычтын иштеши: Муздаткычтар кесүү температурасын төмөндөтүүгө, сүрүлүүнү азайтууга жана таштандыларды тазалоого жардам берет. Натыйжасыз муздаткыч жогорку температурага жана таштандылардын топтолушуна алып келиши мүмкүн, бул кесүү сапатына жана натыйжалуулугуна таасирин тийгизет. Натыйжалуу жана экологиялык жактан таза муздаткычтарды тандоо абдан маанилүү. | Blade сапаты кесүү тактыгына жана жылмакай таасир этет. Натыйжасыз муздаткыч кесүү сапатын жана натыйжалуулугун начарлатып, муздаткычты оптималдуу пайдалануу зарылдыгын баса белгилейт. |
Процессти көзөмөлдөө жана сапатты текшерүү | -Процессти көзөмөлдөө: Реалдуу убакытта мониторинг жүргүзүү жана кесүү процессинде туруктуулукту жана ырааттуулукту камсыз кылуу үчүн негизги кесүү параметрлерин жөнгө салуу. -Сапатты текшерүү: Кесүүдөн кийинки көрүнүштү текшерүү, өлчөмдүү өлчөөлөр жана электрдик көрсөткүчтөрдү текшерүү сапат маселелерин тез арада аныктоого жана чечүүгө жардам берип, кесүүнүн тактыгын жана ырааттуулугун жакшыртат. | Процессти туура көзөмөлдөө жана сапатты текшерүү ырааттуу, жогорку сапаттагы кесүү натыйжаларын камсыз кылууга жана мүмкүн болуучу маселелерди эрте аныктоого жардам берет. |

Кесүү сапатын жакшыртуу
Кесүү сапатын жакшыртуу процесстин параметрлерин, жабдууларды жана материалдарды тандоону, процессти көзөмөлдөөнү жана текшерүүнү эске алган комплекстүү мамилени талап кылат. Кесүү технологияларын үзгүлтүксүз тактоо жана процесс ыкмаларын оптималдаштыруу аркылуу пластиналарды кесүүнүн тактыгын жана туруктуулугун андан ары жогорулатууга болот, бул жарым өткөргүч өндүрүш тармагына ишенимдүү техникалык колдоо көрсөтүү.
#03 Кесүүдөн кийинки иштетүү жана сыноо
3.1 Тазалоо жана кургатуу
Вафли кесилгенден кийин тазалоо жана кургатуу кадамдары чиптин сапатын жана кийинки процесстердин жылмакай жүрүшүн камсыз кылуу үчүн абдан маанилүү. Бул этапта кесүү учурунда пайда болгон кремний калдыктарын, муздатуучу суюктуктун калдыктарын жана башка булгоочу заттарды кылдат тазалоо зарыл. Тазалоо процессинде чиптердин бузулбагандыгын жана кургаткандан кийин коррозия же электростатикалык разряд сыяктуу маселелердин алдын алуу үчүн чиптин бетинде ным калбашы үчүн бирдей маанилүү.
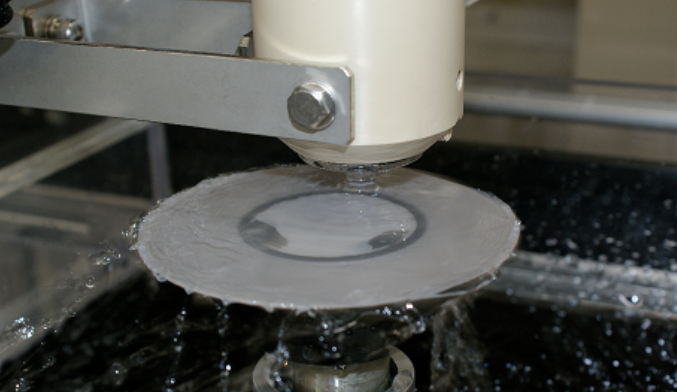
Кесүүдөн кийинки иштетүү: тазалоо жана кургатуу процесси
Процесс кадамы | Мазмун | Таасири |
Тазалоо процесси | -Метод: Тазалоо үчүн ультра үн же механикалык щетка ыкмалары менен бирге атайын тазалоочу каражаттарды жана таза сууну колдонуңуз. | Булгоочу заттардын кылдат тазаланышын камсыздайт жана тазалоо учурунда чиптердин бузулушун алдын алат. |
-Тазалоочу агентти тандоо: Чипке зыян келтирбестен эффективдүү тазалоону камсыз кылуу үчүн вафли материалына жана булгануучу түргө жараша тандаңыз. | Туура агент тандоо натыйжалуу тазалоо жана чип коргоо үчүн негизги болуп саналат. | |
-Параметр башкаруу: Туура эмес тазалоодон келип чыккан сапат маселелерин алдын алуу үчүн тазалоонун температурасын, убактысын жана тазалоо эритмесинин концентрациясын катуу көзөмөлдөңүз. | Контролдор пластинкага зыян келтирбөөгө же булгоочу заттарды калтырбоого жардам берип, ырааттуу сапатты камсыз кылат. | |
Кургатуу процесси | -Салттуу методдор: Табигый аба менен кургатуу жана ысык аба менен кургатуу, эффективдүүлүгү төмөн жана статикалык электрдин топтолушуна алып келиши мүмкүн. | Жайыраак кургатуу жана статикалык көйгөйлөргө алып келиши мүмкүн. |
-Заманбап технологиялар: Чипстер тез кургап, зыяндуу таасирлерден сактануу үчүн вакуумда кургатуу жана инфракызыл кургатуу сыяктуу алдыңкы технологияларды колдонуңуз. | Тезирээк жана натыйжалуу кургатуу процесси, статикалык разряддын же нымдуулукка байланыштуу маселелердин коркунучун азайтат. | |
Жабдууларды тандоо жана тейлөө | -Жабдууларды тандоо: Жогорку өндүрүмдүүлүктөгү тазалоо жана кургатуу машиналары иштетүүнүн эффективдүүлүгүн жакшыртат жана иштетүү учурунда мүмкүн болуучу көйгөйлөрдү жакшы көзөмөлдөйт. | Жогорку сапаттагы машиналар жакшыраак иштетүүнү камсыз кылат жана тазалоо жана кургатуу учурунда каталардын ыктымалдыгын азайтат. |
-Жабдууларды тейлөө: Жабдууларды үзгүлтүксүз текшерүү жана тейлөө анын чиптин сапатына кепилдик берип, оптималдуу иштөө абалында сакталышын камсыз кылат. | Туура тейлөө ишенимдүү жана жогорку сапаттагы иштетүүнү камсыз кылуу, жабдуулардын бузулушуна жол бербейт. |
Кесүүдөн кийинки тазалоо жана кургатуу
Вафли кесилгенден кийин тазалоо жана кургатуу кадамдары татаал жана назик процесстер болуп саналат, алар акыркы иштетүү натыйжасын камсыз кылуу үчүн бир нече факторлорду кылдаттык менен кароону талап кылат. Илимий ыкмаларды жана катаал процедураларды колдонуу менен ар бир чиптин кийинки таңгактоо жана сыноо этаптарына оптималдуу абалда өтүшүн камсыз кылууга болот.
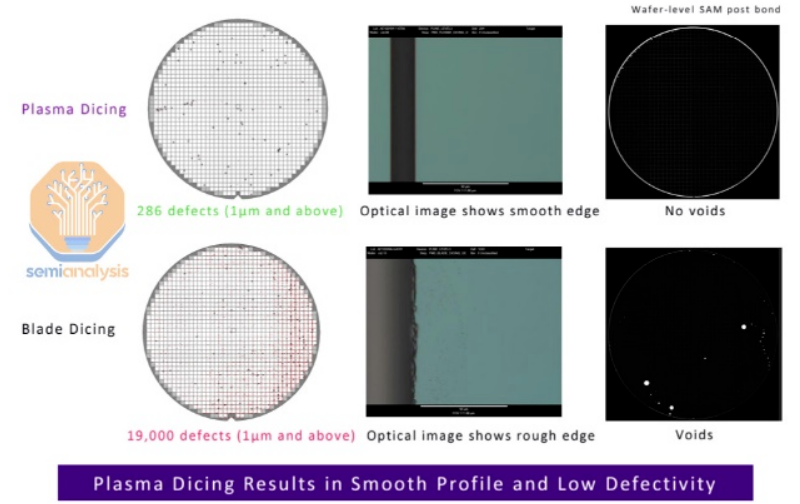
Кесүүдөн кийинки текшерүү жана сыноо
Кадам | Мазмун | Таасири |
Текшерүү кадамы | 1.Визуалдык текшерүү: Чиптин бетиндеги жаракалар, чиптер же булгануу сыяктуу көрүнгөн кемчиликтерди текшерүү үчүн визуалдык же автоматташтырылган текшерүү жабдууларын колдонуңуз. Таштандыларды кетирбөө үчүн физикалык жактан жабыркаган чиптерди тез аныктаңыз. | Процесстин башталышында бузулган чиптерди аныктоого жана жоюуга жардам берет, материалдык жоготууларды азайтат. |
2.Өлчөмү: Чиптин өлчөмдөрүн так өлчөө үчүн так өлчөөчү приборлорду колдонуңуз, кесилген өлчөмү дизайн спецификацияларына туура келүүсүн камсыз кылуу жана аткаруу маселелерин же таңгактоо кыйынчылыктарын алдын алуу. | Чиптердин талап кылынган өлчөмдөрдө болушун камсыздайт, иштин начарлашын же монтаждоо көйгөйлөрүн алдын алат. | |
3.Электр натыйжалуулугун сыноо: Каршылык, сыйымдуулук жана индуктивдүүлүк сыяктуу негизги электрдик параметрлерди баалаңыз, шайкеш келбеген микросхемаларды аныктоо жана аткарууга квалификациялуу микросхемалардын гана кийинки баскычка өтүшүн камсыз кылуу. | Процессте функционалдык жана натыйжалуулук менен текшерилген чиптердин гана алдыга жылышын камсыздайт, кийинки этаптарда иштебей калуу коркунучун азайтат. | |
Сыноо кадамы | 1.Функционалдык тестирлөө: Функционалдык аномалиялары бар микросхемаларды аныктоо жана жок кылуу, чиптин негизги функционалдуулугу белгиленгендей иштеп жатканын текшериңиз. | Кийинки этаптарга өтүүдөн мурун чиптердин негизги операциялык талаптарга жооп беришин камсыздайт. |
2.Ишенимдүүлүк тести: Чыныгы дүйнөдөгү экстремалдык шарттарды симуляциялоо үчүн, адатта, жогорку температурада картаюу, төмөнкү температурада тестирлөө жана нымдуулук тестин камтыган узак убакытка колдонууда же катаал чөйрөдө чиптин иштешинин туруктуулугун баалаңыз. | Чиптердин айлана-чөйрөнүн бир катар шарттарында ишенимдүү иштешин камсыздайт, продуктунун узактыгын жана туруктуулугун жакшыртат. | |
3.Шайкештикти текшерүү: Чиптин башка компоненттер же системалар менен туура иштешин текшерип, туура келбегендиктен эч кандай мүчүлүштүктөр жок же майнаптуулуктун начарлашын текшериңиз. | Шайкештик маселелерин алдын алуу менен реалдуу тиркемелерде үзгүлтүксүз иштешин камсыздайт. |
3.3 Таңгактоо жана сактоо
Вафли кесилгенден кийин, чиптер жарым өткөргүчтөрдү өндүрүү процессинин маанилүү натыйжасы болуп саналат жана аларды таңгактоо жана сактоо этаптары бирдей мааниге ээ. Туура таңгактоо жана сактоо чаралары ташуу жана сактоо учурунда чиптердин коопсуздугун жана туруктуулугун камсыз кылуу үчүн гана эмес, ошондой эле кийинки өндүрүш, сыноо жана таңгактоо этаптарына күчтүү колдоо көрсөтүү үчүн да маанилүү.
Текшерүү жана сыноо этаптарынын кыскача мазмуну:
Вафли кесилгенден кийин микросхемаларды текшерүү жана сыноо кадамдары бир катар аспектилерди камтыйт, анын ичинде визуалдык текшерүү, өлчөмдөрдү өлчөө, электр натыйжалуулугун текшерүү, функционалдык тестирлөө, ишенимдүүлүк тести жана шайкештикти текшерүү. Бул кадамдар бири-бири менен байланышкан жана бири-бирин толуктап, продукциянын сапатын жана ишенимдүүлүгүн камсыз кылуу үчүн бекем тоскоолдукту түзөт. Катуу текшерүү жана тестирлөө жол-жоболору аркылуу потенциалдуу көйгөйлөрдү аныктап, тез арада чечүүгө болот, акыркы продукт кардарлардын талаптарына жана күтүүлөрүнө жооп берет.
Аспект | Мазмун |
Таңгактоо чаралары | 1.Антистатикалык: Таңгактоочу материалдар статикалык электрдин түзүлүштөрдү бузуп же алардын иштешине таасирин тийгизбөө үчүн эң сонун антистатикалык касиеттерге ээ болушу керек. |
2.Нымга чыдамдуу: Таңгактоочу материалдар коррозияга жана нымдуулуктан улам электрдик көрсөткүчтөрдүн начарлашына жол бербөө үчүн жакшы нымдуулукка туруктуу болушу керек. | |
3.Shockproof: Таңгактоочу материалдар чиптерди ташуу учурунда титирөөдөн жана таасирден коргоо үчүн эффективдүү шок жутууну камсыз кылышы керек. | |
Сактоо чөйрөсү | 1.Нымдуулукту көзөмөлдөө: Ашыкча нымдуулуктан же төмөн нымдуулуктан улам келип чыккан статикалык маселелерден улам нымдуулуктун сиңүүсүн жана коррозиясын болтурбоо үчүн нымдуулукту тийиштүү диапазондо катуу көзөмөлдөңүз. |
2.Тазалык: Чиптердин чаң жана аралашмалар менен булганышын болтурбоо үчүн сактоо чөйрөсүн таза сактаңыз. | |
3.Температураны көзөмөлдөө: Ашыкча ысыктан же төмөн температурадан улам пайда болгон конденсация көйгөйлөрүнөн улам тез картаюунун алдын алуу үчүн акылга сыярлык температура диапазонун коюп, температуранын туруктуулугун сактаңыз. | |
Үзгүлтүксүз текшерүү | Сакталган микросхемаларды үзгүлтүксүз текшерип, баалаңыз, визуалдык текшерүүлөрдү, өлчөмдөрдү өлчөө жана потенциалдуу көйгөйлөрдү өз убагында аныктоо жана чечүү үчүн электрдик аткаруу тесттерин колдонуу. Сактоо убактысына жана шарттарына таянып, чиптерди оптималдуу абалда колдонууну пландаштыруу. |
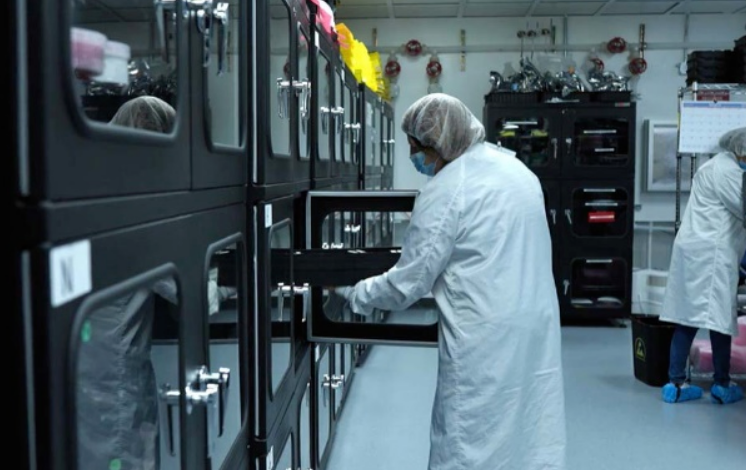
Вафлиди кесүү процессинде микрожарыктар жана бузулуулар маселеси жарым өткөргүчтөрдү өндүрүүдө олуттуу көйгөй болуп саналат. Кесүү стресси бул көрүнүштүн негизги себеби болуп саналат, анткени ал пластинка бетинде майда жаракаларды жана зыянды жаратып, өндүрүштүк чыгымдардын өсүшүнө жана продукциянын сапатынын төмөндөшүнө алып келет.
Бул көйгөйдү чечүү үчүн кесүү стрессин азайтуу жана оптималдаштырылган кесүү ыкмаларын, куралдарын жана шарттарын ишке ашыруу абдан маанилүү. Бычактын материалы, кесүү ылдамдыгы, басым жана муздатуу ыкмалары сыяктуу факторлорго кылдат көңүл буруу микро жаракалардын пайда болушун азайтууга жана процесстин жалпы түшүмүн жакшыртууга жардам берет. Кошумчалай кетсек, лазердик кесүү сыяктуу өнүккөн кесүү технологиялары боюнча жүргүзүлүп жаткан изилдөөлөр бул маселелерди андан ары жеңилдетүүнүн жолдорун изилдеп жатат.
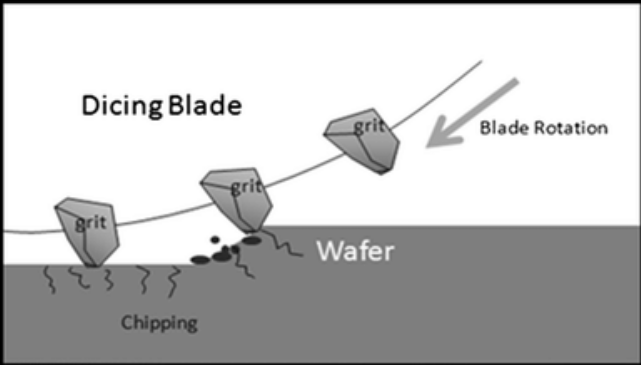
Морт материал катары пластиналар механикалык, термикалык же химиялык стресске дуушар болгондо ички структуралык өзгөрүүлөргө дуушар болуп, микро жаракалардын пайда болушуна алып келет. Бул жаракалар дароо байкалбаса да, өндүрүш процессинин жүрүшүнө жараша алар кеңейип, катуураак зыян келтириши мүмкүн. Бул маселе кийинки таңгактоо жана тестирлөө этаптарында өзгөчө көйгөйлүү болуп калат, мында температуранын өзгөрүшү жана кошумча механикалык стресстер бул микро жаракалардын көрүнөө сыныктарга айланып, чиптин бузулушуна алып келиши мүмкүн.
Бул коркунучту азайтуу үчүн, кесүү ылдамдыгы, басым жана температура сыяктуу параметрлерди оптималдаштыруу аркылуу кесүү процессин кылдаттык менен көзөмөлдөө зарыл. Лазердик кесүү сыяктуу азыраак агрессивдүү кесүү ыкмаларын колдонуу пластинкадагы механикалык стрессти азайтып, микро жаракалардын пайда болушун азайтат. Кошумчалай кетсек, пластинкаларды кесүү процессинде инфракызыл сканерлөө же рентгендик сүрөт тартуу сыяктуу алдыңкы текшерүү ыкмаларын ишке ашыруу бул алгачкы этаптагы жаракаларды андан ары зыянга учуратканга чейин аныктоого жардам берет.
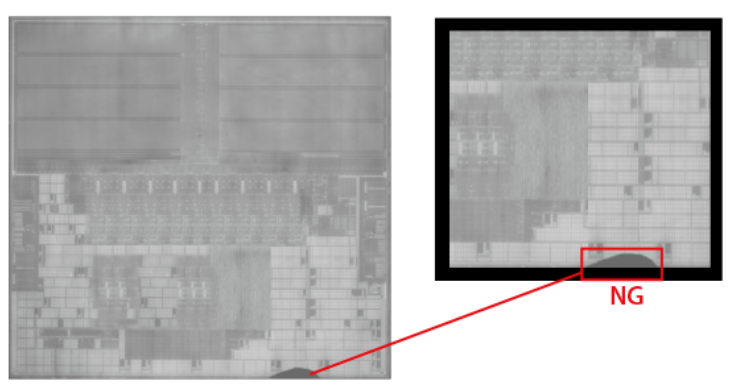
Вафлидин бетине зыян келтирүү чиптин иштешине жана ишенимдүүлүгүнө түздөн-түз таасирин тийгизиши мүмкүн болгондуктан, кесүү процессинде олуттуу тынчсыздануу жаратат. Мындай зыян кесүүчү шаймандарды туура эмес колдонуудан, туура эмес кесүүчү параметрлерден же пластинкага мүнөздүү болгон материалдык кемчиликтерден келип чыгышы мүмкүн. Себептерине карабастан, бул бузулуулар чынжырдын электр каршылыгынын же сыйымдуулугунун өзгөрүшүнө алып келиши мүмкүн, бул жалпы иштөөгө таасир этет.
Бул маселелерди чечүү үчүн эки негизги стратегия изилденип жатат:
1.Оптимизациялоо кесүүчү куралдарды жана параметрлерди: Курч бычактарды колдонуу, кесүү ылдамдыгын тууралоо жана кесүү тереңдигин өзгөртүү менен, кесүү процессинде стресстин концентрациясын минималдаштырууга болот, ошентип зыяндын потенциалын азайтууга болот.
2. Жаңы кесүү технологияларын изилдөө: Лазердик кесүү жана плазма кесүү сыяктуу өркүндөтүлгөн ыкмалар вафлиге келтирилген зыяндын деңгээлин төмөндөтүү менен бирге жакшыртылган тактыкты сунуштайт. Бул технологиялар пластинкадагы жылуулук жана механикалык стрессти азайтып, жогорку кесүү тактыгына жетүү жолдорун табуу үчүн изилденип жатат.
Жылуулук таасиринин аймагы жана анын натыйжалуулугуна тийгизген таасири
Лазердик жана плазмалык кесүү сыяктуу термикалык кесүү процесстеринде жогорку температура сөзсүз түрдө вафлидин бетинде термикалык таасир зонасын түзөт. Температура градиенти маанилүү болгон бул аймак материалдын касиеттерин өзгөртүп, чиптин акыркы иштешине таасир этет.
Жылуулук таасир эткен аймактын таасири (ТАЗ):
Кристаллдын структурасын өзгөртүү: Жогорку температурада пластинкадагы атомдор кристалл түзүмүндө бурмалоолорго алып келиши мүмкүн. Бул бурмалоо материалды алсыратат, анын механикалык күчүн жана туруктуулугун төмөндөтөт, бул колдонуу учурунда чиптин бузулуу коркунучун жогорулатат.
Электрдик касиеттердеги өзгөрүүлөр: Жогорку температуралар жарым өткөргүч материалдардагы ташуучунун концентрациясын жана кыймылдуулугун өзгөртүп, чиптин электр өткөргүчтүгүнө жана ток өткөрүүнүн натыйжалуулугуна таасирин тийгизет. Бул өзгөртүүлөр чиптин иштешинин төмөндөшүнө алып келиши мүмкүн, бул анын максатына жараксыз болушу мүмкүн.
Бул таасирлерди жумшартуу үчүн, кесүү учурунда температураны көзөмөлдөө, кесүү параметрлерин оптималдаштыруу жана муздатуу учактары же кайра иштетүүдөн кийинки дарылоо сыяктуу ыкмаларды изилдөө жылуулук таасиринин көлөмүн азайтуу жана материалдын бүтүндүгүн сактоо үчүн маанилүү стратегия болуп саналат.
Жалпысынан алганда, микрожарыктар да, термикалык таасир зоналары да пластинкаларды кесүү технологиясында чечүүчү кыйынчылыктар болуп саналат. Технологиялык жетишкендиктер жана сапатты көзөмөлдөө чаралары менен бирге изилдөөнү улантуу жарым өткөргүч продукциянын сапатын жакшыртуу жана алардын рыноктогу атаандаштыкка жөндөмдүүлүгүн жогорулатуу үчүн зарыл болот.
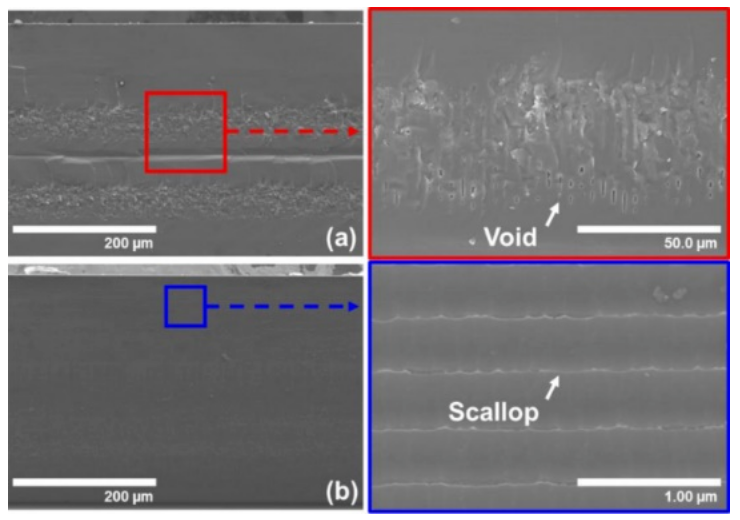
Жылуулук таасир зонасын көзөмөлдөө боюнча чаралар:
Кесүү процессинин параметрлерин оптималдаштыруу: Кесүү ылдамдыгын жана күчүн азайтуу жылуулук таасири зонасынын (TAZ) өлчөмүн эффективдүү азайта алат. Бул кесүү процессинде пайда болгон жылуулуктун көлөмүн көзөмөлдөөгө жардам берет, бул вафлидин материалдык касиеттерине түздөн-түз таасирин тийгизет.
Өркүндөтүлгөн муздатуу технологиялары: Суюк азотту муздатуу жана микрофлюиддик муздатуу сыяктуу технологияларды колдонуу жылуулук таасир этүүчү аймактын диапазонун олуттуу чектей алат. Бул муздатуу ыкмалары жылуулукту натыйжалуураак таркатууга жардам берет, ошентип, вафлидин материалдык касиеттерин сактап, термикалык зыянды азайтат.
Материалды тандоо: Окумуштуулар көмүртек нанотүтүкчөлөрү жана графен сыяктуу жаңы материалдарды изилдеп жатышат, алар эң сонун жылуулук өткөрүмдүүлүккө жана механикалык күчкө ээ. Бул материалдар микросхемалардын жалпы иштешин жакшыртуу менен бирге жылуулук таасири зонасын азайта алат.
Кыскача айтканда, жылуулук таасири зонасы термикалык кесүү технологияларынын сөзсүз натыйжасы болсо да, аны оптималдаштырылган иштетүү ыкмалары жана материалды тандоо аркылуу натыйжалуу башкарууга болот. Келечектеги изилдөөлөр, кыязы, пластинкалардын эффективдүү жана так кесилишине жетишүү үчүн термикалык кесүү процесстерин тактоо жана автоматташтырууга багытталган.

Баланс стратегиясы:
Вафлидин түшүмдүүлүгү менен өндүрүштүн эффективдүүлүгүнүн ортосундагы оптималдуу баланска жетишүү вафлиди кесүү технологиясында тынымсыз көйгөй болуп саналат. Өндүрүүчүлөр рационалдуу өндүрүш стратегиясын жана процесстин параметрлерин иштеп чыгуу үчүн рыноктук суроо-талап, өндүрүштүк чыгымдар жана продукциянын сапаты сыяктуу бир нече факторлорду эске алышы керек. Ошону менен бирге прогрессивдуу кесуучу жаб-дууларды ишке киргизуу, оператор-лордун чеберчилигин жогорулатуу жана сырьёнун сапатына контролдукту кучетуу ендуруштун эффективдуулугун жогорулатуу менен бирге тушумдуулукту сактоо же ал тургай жакшыртуу учун маанилуу.
Келечектеги чакырыктар жана мүмкүнчүлүктөр:
Жарым өткөргүч технологиясын өркүндөтүү менен, пластинкаларды кесүү жаңы кыйынчылыктарга жана мүмкүнчүлүктөргө туш келет. Чиптин өлчөмдөрү кичирейген сайын жана интеграция көбөйгөн сайын кесүү тактыгына жана сапатына болгон талаптар кыйла өсөт. Ошол эле учурда, өнүгүп келе жаткан технологиялар вафли кесүү ыкмаларын өнүктүрүү үчүн жаңы идеяларды берет. Өндүрүүчүлөр рыноктун динамикасына жана технологиялык тенденцияларына ылайыкташып, рыноктун өзгөрүшүнө жана технологиялык талаптарга жооп берүү үчүн өндүрүш стратегияларын жана процесстин параметрлерин тынымсыз тууралап жана оптималдаштырып турушу керек.
Жыйынтыктап айтканда, рыноктун суроо-талабын, өндүрүштүн баасын жана продукциянын сапатын эске алуу менен, ошондой эле алдыңкы жабдууларды жана технологияны киргизүү, оператордун квалификациясын жогорулатуу жана чийки заттык көзөмөлдү күчөтүү аркылуу өндүрүүчүлөр пластинанын түшүмдүүлүгү менен өндүрүштүн эффективдүүлүгүнүн ортосундагы эң жакшы баланска жетише алышат, бул натыйжалуу жана жогорку сапаттагы жарым өткөргүч продукциясын өндүрүүгө алып келет.
Келечектеги божомол:
Тез технологиялык прогресс менен жарым өткөргүчтөрдүн технологиясы болуп көрбөгөндөй темп менен өнүгүп жатат. Жарым өткөргүчтөрдү өндүрүүдө маанилүү кадам катары, пластинкаларды кесүү технологиясы кызыктуу жаңы өнүгүүлөргө даяр. Келечекке көз чаптырып, пластинка кесүү технологиясы тактык, эффективдүүлүктү жана өздүк наркын олуттуу жакшыртууга жетишип, жарым өткөргүч өнөр жайынын тынымсыз өсүшүнө жаңы күч-кубат берет деп күтүлүүдө.
Тактыгын жогорулатуу:
Жогорку тактыкка умтулуу менен, вафли кесүү технологиясы учурдагы процесстердин чегин тынымсыз түртөт. Кесүү процессинин физикалык жана химиялык механизмдерин терең изилдөө жана кесүү параметрлерин так көзөмөлдөө менен, схемаларды долбоорлоонун барган сайын татаал талаптарын канааттандыруу үчүн кесүүнүн жакшы натыйжаларына жетишилет. Мындан тышкары, жаңы материалдарды жана кесүү ыкмаларын чалгындоо түшүмдүүлүктү жана сапатты бир топ жакшыртат.
Натыйжалуулукту жогорулатуу:
Вафли кесүүчү жаңы жабдуулар акылдуу жана автоматташтырылган дизайнга багытталат. Башкаруунун прогрессивдуу системаларын жана алгоритмдерин ишке киргизуу жабдууларды ар кандай материалдарды жана конструкциялык талаптарды канааттандыруу учун кесуу параметрлерин автоматтык турде тууралоого мумкундук берет, ошентип ендуруштун эффективдуулугун бир кыйла жогорулатат. Эффективдүүлүктү жогорулатууда көп катмарлуу кесүү технологиясы жана бычакты тез алмаштыруу системалары сыяктуу инновациялар чечүүчү роль ойнойт.
Чыгымдарды азайтуу:
Чыгымдарды кыскартуу пластинкаларды кесүү технологиясын өнүктүрүүнүн негизги багыты болуп саналат. Жаңы материалдар жана кесүү ыкмалары иштелип чыккандыктан, жабдуулардын чыгымдарын жана техникалык тейлөөгө кеткен чыгымдарды натыйжалуу көзөмөлдөө күтүлүүдө. Кошумчалай кетсек, өндүрүш процесстерин оптималдаштыруу жана калдыктарды азайтуу өндүрүш учурундагы калдыктарды андан ары азайтат, бул жалпы өндүрүштүк чыгымдардын азайышына алып келет.
Акылдуу өндүрүш жана IoT:
Акылдуу өндүрүш менен нерселердин Интернети (IoT) технологияларын интеграциялоо пластинкаларды кесүү технологиясына трансформациялык өзгөрүүлөрдү алып келет. Түзмөктөр ортосунда өз ара байланыш жана маалымат алмашуу аркылуу өндүрүш процессинин ар бир кадамын реалдуу убакыт режиминде көзөмөлдөөгө жана оптималдаштырууга болот. Бул өндүрүштүн эффективдүүлүгүн жана продукциянын сапатын гана жакшыртпастан, компанияларга рыноктун так болжолдоосун жана чечимдерди кабыл алууну колдоону камсыздайт.
Келечекте, пластинка кесүү технологиясы тактык, натыйжалуулук жана наркы боюнча көрүнүктүү ийгиликтерди жаратат. Бул жетишкендиктер жарым өткөргүч өнөр жайынын тынымсыз өнүгүшүнө түрткү берет жана адамзат коомуна көбүрөөк технологиялык инновацияларды жана ыңгайлуулуктарды алып келет.
Посттун убактысы: 2024-жылдын 19-ноябрына чейин